top of page

abbeo Materials
Application method textile
The application of the abbeo hygiene protection products takes place during the production of the textile itself, i.e. at the very beginning of the production chain. On the one hand, this has to do with cost savings - no additional work step is necessary - and on the other hand also with security in terms of durability and functionality of the finish, which is individually adapted to the respective textile and its physical properties (density, weight, fiber type, etc.) according to the protection objective .
In principle, the abbeo application can be carried out with the following work steps:
pretreatment
(desizing, bleaching, optical brightening etc.
To dye
(as an additive in the dye bath, in the continuous work process or in the exhaust process)
finishing
(when using plasticizers, finishes, fluorocarbons, hydrophilic agents, etc.)
​ ​
Which work step is ideal for the application of the hygiene protection agent depends on the formulations of the individual areas and the other textile chemicals used and their compatibility.
Our abbeo technicians will advise you professionally and develop the appropriate recipe with you and your textile manufacturer.
Foulard application
(Continuous application method)
In the continuous process, most of the work steps are arranged one after the other, continuously and the processing of the textile takes place in one pass. Textile auxiliaries and products are used, which are "forced" to be applied to the textile surface by immersion in a chemical bath (liquor). The calculation of the necessary roller pressure regulates how much of the liquor is squeezed off again and thus how much of the textile auxiliary is applied to the textile.

2
3
4
1
Simple scheme of a 2-roller foulard.
The fabric web (1) runs over several rollers into the application bath (2) and then over squeezing rollers (3), the pressure of which defines the exact absorption of the application liquor and thus of the hygiene protection product. The textile is then dried and processed using a drying system (4) (IR dryer or condensers).

Upstream and downstream are the spools (rollers with lengths of fabric) on which the textile is removed or rolled up and stored.

Example of a complete continuous system (Monforts) in which application, drying, condensing or, depending on requirements, steaming can also take place for the fixing process on the textile.
Extract Application Procedure
(discontinuous application process)
The exhaust process differs from the foulard process in that textile auxiliaries and chemicals are used which have the characteristics of their own ability to be lifted onto the textile, i.e. they are absorbed from the liquor itself onto the fiber and bind to the surface. This behavior can be favored by various parameters such as temperature, pH value, addition of salts and kinetics (movement of the liquor). It is also particularly important here to have a pretreated, hydrophilic (absorbent) textile material. Subsequent work steps such as rinsing, drying, steaming, condensing and finishing must be carried out in individual work processes.
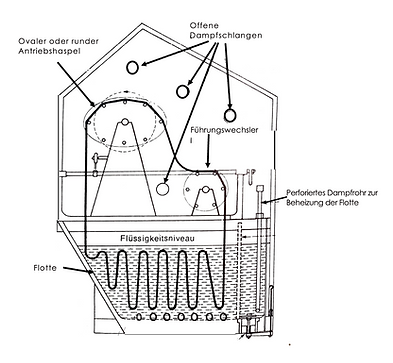
Schematic of a reel skid
The fabric web is driven by a reel and pulled through the liquor with the hygiene protection agent. The direction of material transport is changed regularly to ensure that the products are drawn up evenly. The liquor is heated by steam and cooled by cooling water. Depending on the time, this process runs for several hours until the extract is complete. The reel vat can be operated normally up to boiling temperature, or in a closed system also at high temperatures (up to 130°C for synthetic fibres).
Jet (Airflow)
The jet is a closed system which can also be applied under HT conditions (high temperature). The textile is passed through a nozzle (1) which applies a mixture of air and liquor to the textile at high speed, pulling it forward. The transport is supported by a small reel (2). Due to the cylindrical shape of the jet, the textile remains lying in the liquor (3) after passing through the nozzle until the next passage is due. Textile auxiliaries are again applied to the surface.
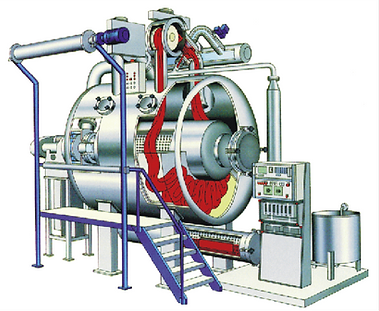
1
2
3
packing apparatus
Textiles have different appearances and can in principle be finished in any form. Depending on the configuration, a packing device offers an efficient and easily controllable system for permanently protecting textiles against bacteria and germs.


Equipment of cross-wound bobbins
When manufacturing yarn, it is wound onto spools (cones) in a cross structure. Many kilometers of yarn are stored on a Kone for each yarn and fiber type. In a special packing device, the spools are stacked one on top of the other and sealed in a closed system. The liquor is pressed through perforated tubes from the inside through the yarn layer of the spool to the outside. The flow direction can also alternate. This means that all articles that are later made from this yarn are already hygienically protected.
Finishing of yarn skeins
If the yarn is not wound up on cones, it can also be further processed as yarn skeins. This is often the case when it comes to thicker, coarser yarns or they are not suitable for winding. The skein dyeing or finishing apparatus is designed in such a way that the skeins come into contact with the liquor while hanging in the apparatus and are treated.
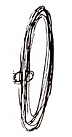

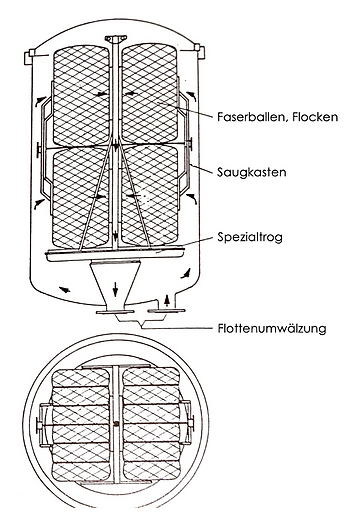

equipment of flakes
In its loosest form, the textile is in the form of a flock. It is often wool, but also cotton after it has been picked from the tree or cellulose fibers after they have been manufactured. Here, too, the concept is largely identical to that of the other packing devices, the tufts are treated and finished in bales in the boiler.


Equipment of winding bodies
For warp yarns used in weaving or for wound textile webs, which are rolled up on a winding beam (perforated tube through which the liquor is pumped) and finished in a closed system.

bottom of page